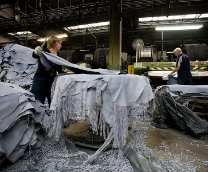
Как это сделано ютюб
158 постов
158 постов
8 постов
277 постов
77 постов
110 постов
7 постов
3 поста
23 поста
21 пост
19 постов
2 поста
4 поста
2 поста
4 поста
2 поста
2 поста
3 поста
6 постов
За год работы в казино в свой адрес можно услышать мата больше, чем за всю остальную жизнь, заодно выучить много идиоматических выражений и крылатых фраз. Мат - повседневный язык в стаффе (комнате персонала казино)
Угрозы искалечить или убить чаще всего пустой звук, на улице игроки притворяются, что не знают вас или разговаривают дружелюбно.
Казино не обманывает игроков, коэффициенты выигрышей в азартных играх итак устроены в пользу казино. Обмануть или обокрасть может сосед по столу или нечистый на руку дилер (крупье), но это редкость, потому что везде камеры и прослушки.
Игровые автоматы чаще всего перепрошиваются владельцами на самый минимальный выигрыш (так было в России по крайней мере). Игровые автоматы не равно казино, казино это игры за столами, автоматы могут быть в каком-нибудь месте, которое не будет считаться за казино. Менеджеры казино не заинтересованы сознательно обманывать игроков, это рано или поздно выявится, потому что игроки тоже не слепые и делятся друг с другом инфой.
После года работы напрочь ломаются биологические часы, потому что смены то 2 дня в день, то два дня в ночь, а то и сутки.
Сон на работе может стоить штрафа в дневной заработок.
Каждый день на работе в казино это день сурка, и такой день может тянуться годами.
Все нужные для дилера навыки приобретаются меньше чем за полгода, далее никакого развития в этой профессии нет, только стать пит-боссом (начальников над сменой) или менеджером.
До сих пор в России есть подпольные казино, хозяева которых платят взятки органам за крышу. Я работал в таком.
За ночь дилер может проиграть полмиллиона или миллион, и ему ничего за это не будет, если конечно он не в сговоре с игроком (такое очень редко, но бывает).
Игрок никогда не уйдет из казино, если сходу выиграет большую сумму. Не наигрался, да и карта прет, как можно уходить? Ну и конечно как правило все проигрывает.
Дилер может подряд попасть в один и тот же номер на рулетке 3 раза, раздать за смену все комбинации в покер, и увидеть такое, что придумывают сценаристы. Учитывая, что он раздает карты и пускает шарик по рулетке тысячи раз возможно все (но очень редко).
Карманы штанов и рубашек обязательно должны быть зашиты, чтобы не воровали фишки (но некоторых ушлых дилеров это не останавливало.
Если игрок выигрывает больше, чем проиграл, то его вносят в черный список. По каждому игроку ведется статистика.
В казино игрокам разрешено курить, потому некурящий дилер в этом месте вдохнет больше сигаретного дыма, чем за всю остальную жизнь. Ну и рабочая одежда пропахнет дымом очень сильно.
Задавайте вопросы, может вспомню еще что, и буду добавлять пункты
У кого без впн не работает скоро выгружу на доступных платформах.
Про грязную лапшу публиковал пост пару лет назад - Как делают грязную лапшу в Индонезии
Познавательные посты и ролики о том как устроены вещи, как работают и как сделаны публикуются в сообществе Как это сделано, присоединяйтесь, там много интересного!
Поддержать выпуск новых репортажей можно по ссылке. Спасибо!
https://pay.cloudtips.ru/p/19c62f42
Снимал на Хакасском алюминиевом заводе в Саяногорске. Зачем их меняют, что такое аноды и электролизеры рассказывал ранее тут - Как выплавляют алюминий
Кому сложно на ютюбе можете глянуть на бусти за символический донат, заодно поддержите создание новых видео и фоторепортажей на производственную тематику. - https://boosty.to/kaketosdelano/posts/63f955da-e1f0-41ca-9f2...
В декабре снял материал про выплавку алюминия, гляньте, поддержите комментарием, плюсом или донатом, как хотите. Скоро выложу на вк.
Познавательные посты и ролики о том как устроены вещи, как работают и как сделаны публикуются в сообществе Как это сделано, присоединяйтесь, там много интересного!
Поддержать выпуск новых репортажей можно по ссылке. Спасибо!
https://pay.cloudtips.ru/p/19c62f42
Факт № 35
Наверняка многие из вас знают, что длина марафонской дистанции составляет 42км 195 метров. Согласно легенде (точнее записям философа Плутарха) примерно такое расстояние пробежал от поля битвы при Марафоне до Афин греческий воин по имени Евкл в 490 году до н. э. чтобы возвестить о победе греков.
В этой легенде только один факт является историческим - битва при Марафоне между греками и персами. Остальное никак исторически не подтверждено, то есть вероятнее всего выдумка Плутарха, который описал этот случай спустя 550 лет после битвы.
Неправдой является и расстояние в 42 км 195 метров между полем битвы и Афинами. Созданный перед первой современной Олимпиадой в 1896 международный олимпийский комитет измерил фактическую длину дистанции от поля битвы в Марафоне до Афин, и она оказалась равной 34,5 км. Аж на 8 км короче, чем современная). Почему так?
Длина пробега не была изначально фиксированной, и выбиралась произвольно. Важным было только то, что все спортсмены бежали по одному и тому же маршруту, который зависел от маршрута, выбранного на разных Играх.
На первой Олимпиаде в 1896 году длина составляла 40 км. А вот уже в 1908 году в Лондоне ее увеличили до 42 км 195 метров. Тогда дистанция была увеличена специально для того, чтобы королевская семья могла с удобством наблюдать за пробегом с балкона Виндзорского замка.
На следующей Олимпиаде в 1912 году дистанцию опять уменьшили до 40 км 200 м, а в 1920 увеличили до 42 км 750 м. Наконец, в 1921 году Международной любительской легкоатлетической федерацией была окончательно установлена официальная дистанция марафонского забега, которая используется и по сей день — 42 километра 195 метров.
Всего на первых семи Олимпиадах было 6 различных марафонских дистанций от 40 до 42,75 км
Вот так, благодаря прихоти британской королевской семьи дистанция составляет не 34.5, и не 40 км, а 42км 195 метров.
Факты узнаю и пишу сам в своем телеграм канале - https://t.me/uznalsegodnya
Подписывайтесь и поддержите, если нравится такой формат!
https://pay.cloudtips.ru/p/19c62f42
Факт № 34
Еще со времен школы мы выучили тот факт, что самый большой остров на нашей планете - Гренландия, но это морской остров, а какой речной остров самый большой? Этот вопрос почему-то упрямо игнорируют на уроках географии. Видимо сами учителя не знают об этом.
А самый большой речной остров находится в Южной Америке, на территории Бразилии. Называется он Бананал, наверное потому что похож по форме на банан.
На карте можно увидеть масштабы, он довольно внушительный. Остров расположен в среднем течении реки Арагуаи, его длина доходит до 300 км, ширина — до 160 км. Площадь Бананала составляет 19 162 км², что больше, чем такие страны как Фиджи, Кувейт, Катар и Черногория.
Там же, в Южной Америке находится еще один остров рекордсмен - Маражо, который находится в устье реки Амазонка. Он вдвое больше, чем Бананал. Длина острова составляет 220 км, ширина до 150км. Площадь — 40 100 км². Но так как с одной стороны он омывается Атлантическим океаном, то не считается полноценно речным. Площадь Маражо сравнима с Рязанской областью, или с такими странами как Швейцария и Нидерланды.
Факты узнаю и пишу сам в своем телеграм канале - https://t.me/uznalsegodnya
Подписывайтесь и поддержите, если нравится такой формат!
https://pay.cloudtips.ru/p/19c62f42
Факт № 22
Несмотря на то, что я вырос в самой высокогорной республике Кавказа на флаге которой изображен Эльбрус, об этом факте я узнал на днях. И он касается гор, которые не стали вулканами.
Оказывается для гор, которые вспучились, но не извергли в свое время магму существуют такой геологический термин - "лакколит".
Гора Аю-Даг в Крыму
Лакколитами называют не все горы, у которых нет жерла (или кратера), а только те, у которых под толщей горных пород протекала ничем не закончившаяся вулканическая деятельность.
Машук, находится в городской черте Пятигорска
Магма внутри таких гор застыла миллионы лет назад, превратилась в камень и такая гора никогда уже не станет вулканом.
Самые известные горы-лакколиты в России это горы Пятигорска - Бештау, Машук (и еще 17 гор КавМинвод), а также крымская гора Аю-Даг.
Бештау
Все факты пишу сам в этом телеграм-канале - https://t.me/uznalsegodnya/100
Если понравилось можете стимулировать на другие интересные факты о которых вы не знали.
https://pay.cloudtips.ru/p/19c62f42
Остальные факты, которые я публиковал в пикабу:
Зубы Джорджа Вашингтона
Античная помойка - сокровищница для археологов. Монте Тестаччо
Почему Колизей наполовину разрушен или не достроен?
Антиминимализм или клаттеркор
Факт № 21
Оказывается, то нагромождение вещей в наших комнатах и на стенах, который многие из нас считают бардаком называется клаттеркор и считается стилем у дизайнеров.
Однако, если вашу комнату чаще всего украшают грязные носки на полу, не собранная одежда на компьютерном кресле и прочий беспорядок, который просто захламляет ваше пространство, это все-таки бардак.
Под стиль клаттеркор подпадает упорядоченная демонстрация дорогих вам вещей, в которых есть история, и прежде всего ваши воспоминания.
Это могут быть ряды книг на полках, старинные открытки, постеры с любимыми исполнителями или фильмами, статуэтки, экзотические маски, коллекции игрушек, рисунки, и множество домашних растений.
Я больше люблю минимализм, и стараюсь убрать все лишние вещи в ящики и на полки, но такое ощущение, что стиль клаттеркор со временем потихоньку наползает на мой минимализм.
Кстати, поделитесь в коментах своими стилями комнаты, интересно глянуть)
Все факты пишу сам в этом телеграм-канале - https://t.me/uznalsegodnya/91
Если понравилось можете стимулировать на другие интересные факты о которых вы не знали.
https://pay.cloudtips.ru/p/19c62f42
Остальные факты, которые я публиковал в пикабу:
Зубы Джорджа Вашингтона
Античная помойка - сокровищница для археологов. Монте Тестаччо
Почему Колизей наполовину разрушен или не достроен?