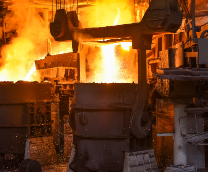
Металлургия
11 постов
В последнее воскресенье августа в России отмечается День шахтёра. Горная отрасль — одна из стратегически важных в отечественной экономике. От труда шахтёров зависят энергетическая и экономическая безопасность России, статус крупного экспортёра и благополучная жизнь людей в каждом регионе.
Раньше добыча руды и угля во многом была тяжёлым ручным трудом. Теперь на смену грубой силе приходят современные технологии: рутинную, опасную работу выполняют новые машины. Задача же человека всё больше смещается в сторону управления и контроля.
Расскажем о достижениях науки и техники, без которых невозможно представить современную добычу полезных ископаемых.
Вкалывают роботы, а не человек
Когда-то руду из шахт поднимали вручную. Сегодня на себя опасную работу берут автономные комплексы. К ним относятся беспилотные карьерные самосвалы, буровые установки для бурения скважин, подземные погрузочно-доставочные машины, а также роботизированные экскаваторы и землеройная техника. В ряде случаев используются и лёгкие рельсовые комплексы, позволяющие перевозить материалы под землёй.
Студенты НИТУ МИСИС тоже не отстают от старших коллег. Ранее они создали робота «Марк» для горнодобывающего предприятия «Норильский никель» — мобильную платформу размером 120×120×80 см для прохождения по подземным выработкам. Каждый его колёсный модуль обладает собственным двигателем и может менять клиренс (расстояние между нижней частью машины и землёй), а платформа снабжена датчиком для 3D моделирования горной выработки. Такой робот может выполнять маркшейдерские съёмки без участия человека.
Аддитивные технологии давно применяются в аэрокосмической, автомобильной и медицинской отраслях, но знали ли вы, что они также активно внедряются и в горную индустрию? 3D-печать позволяет создавать высокопрочные детали для горной техники, например компоненты буровых установок и экскаваторов. Преимущества очевидны: сложные конструкции требуют меньших затрат. Например, в НИТУ МИСИС разработан новый метод 3D-печати, который позволяет создавать металлические детали, устойчивые к высоким температурам и давлению.
Автономные горные системы становятся важным направлением в развитии горной отрасли. Есть компании, которые, например, уже создали беспилотные грузовики, экскаваторы и буровые установки, что позволило горнодобывающим предприятиям снизить затраты на 15% и значительно повысить безопасность на рабочих местах.
Некоторым предприятиям важна независимость от конкретных производителей. Для таких случаев существуют системы, которые можно установить на различные машины без привязки к одному разработчику. Примеры таких решений: Nav/Mobius, Teleop Auto и AutoMine.
Тренажёры виртуальной реальности
Важнее техники и экипировки может быть только подготовка самого шахтёра. Если раньше обучаться приходилось на практике или в учебных классах, то сейчас применяются виртуальные тренажёры. В таких симуляторах специалист отрабатывает алгоритмы действий при экстренных ситуациях (включение самоспасателя, поиск резервного выхода, использование пожарного инвентаря и т. д. при выбросе метана, пожаре, обрушении) без реальной опасности. В НИТУ МИСИС, например, есть лаборатория BELAZ-VR, где представлены тренажёры для работы с карьерными самосвалами. В России всего две таких.
Электромобили в шахтах
Дизельные грузовики и экскаваторы постепенно заменяются электрическими машинами: они снижают выбросы, шум и требования к вентиляции подземных объектов (труды основоположника отечественной научной школы рудничной вентиляции Александра Скочинского, однако, актуальности не теряют). Так, уже существует шахтный электромобиль «Крот Электро». Он подходит как для перевозки людей, так и для грузов. Инженеры отказались от коробок передач в пользу бесшумных токовых приводов. Автономная система управления на базе ROS (операционная система для роботов) самостоятельно прокладывает маршрут, строит карту шахты и реагирует на препятствия. В перспективе парк электротранспорта позволит одному диспетчеру дистанционно управлять десятками таких машин.
Системы контроля над шахтой
Повышение безопасности на объектах — первоочередная задача. На смену традиционным методам отвода воздуха пришла автоматизированная система вентиляции. Они собирают данные с анемометров и датчиков, установленных по всей шахте, и автоматически контролируют подачу воздуха. В специальных диспетчерских центрах можно отследить параметры для каждого участка. Это помогает своевременно реагировать на опасные скопления газов.
Учёные НИТУ МИСИС разработали агрегат, который точечно воздействует на стенки скважин, помогает проводить их разрыв и развивать трещины вглубь массива, чтобы снизить риски выброса метана. Это сможет предотвратить несчастные случаи, спасти жизни шахтерам и техническому персоналу угле- и горнодобывающих компаний. Также существуют вакуумные метанодренажные установки и мобильные системы дегазации, которые забирают метан ещё до того, как он попадёт в горные выработки.
Российские компании также разрабатывают современные шахтные системы безопасности, которые составляют серьёзную конкуренцию мировым аналогам. Эти комплексы позволяют в реальном времени отслеживать концентрацию метана и других газов, уровень пыли, скорость воздушных потоков, температуру и влажность, автоматически управляют вентиляцией и оборудованием, а также обеспечивают связь и оповещение в аварийных ситуациях. Главная особенность — непрерывное определение местоположения шахтёров с точностью до метра, что жизненно необходимо в экстренных ситуациях.
Техногенные землетрясения можно предсказать
Знали ли вы, что можно запатентовать способ оценки максимально возможной магнитуды землетрясений на территориях, где происходит освоение недр и ведутся горные работы? А это уже сделано. В научном центре Горного института НИТУ МИСИС «Геодинамика и геоэкология недр» изучается реакция горного массива на техногенные воздействия. В том числе используется научная концепция, предполагающую наличие в земной коре особого слоя переменной мощности, в котором породы находятся в предельно напряженном состоянии. Понимание этих процессов имеет решающее значение для горнодобывающей деятельности и эксплуатации ресурсов.
В заключение
Сегодня шахтёрский труд уже не сводится лишь к физической работе — он становится частью большого комплекса высокотехнологичных автономных систем. Но смысл его остаётся неизменным: именно благодаря шахтёрам общество получает доступ к необходимым для повседневной жизни ресурсам. Поэтому День шахтёра — это напоминание нам с вами о том, что развитие страны невозможно без тех, кто осваивает глубины Земли, ведь каждый новый подъём к вершинам науки, техники и промышленности начинается с того, что кто-то спускается в шахту.
20 июля в России отмечается День металлурга. Поговорим о том, как металлическая 3D‑печать переходит из разряда перспективных экспериментов в полноценную производственную практику.
Аддитивные технологии позволяют создавать детали сложной формы (с внутренними каналами, тонкими стенками и т. п.) там, где раньше требовались сборные узлы. Турбинные лопатки, имплантаты, детали летательных аппаратов — всё чаще на них появляются характерные штриховки послойной печати.
Сегодня 3D‑печать металлами востребована в самых разных отраслях — от нефтегазовой и космической отраслей до авиа- и судостроения.
Технология позволяет взглянуть на металлургию под другим углом: например, компоновка элементов с «узорчатой» внутренней структурой заметно снижает массу изделия, а необходимые запчасти можно изготовить по мере необходимости без длительной доставки и складирования запасных частей.
За этим стоит глубокая научная трансформация, о которой сегодня пойдёт речь.
Учёные отмечают, что по качеству напечатанные детали зачастую сравнимы с обычными, а в некоторых случаях и вовсе превосходят их благодаря оптимизированной структуре. При этом 3D-печать позволяет сократить затраты на оснастку, уменьшить объёмы отходов и ускорить выход новых изделий на рынок.
Эксперты прогнозируют рост объёма мирового рынка аддитивных технологий до ~83,6 млрд долларов к 2030 году. В России рынок за 1 год уже достиг 4,5 млрд рублей и, по прогнозам Минпромторга, вырастет до ~58 млрд к 2030 году.
Именно поэтому металлургические предприятия активно инвестируют средства в разработку 3D-принтеров и подготовку специалистов.
Что уже в ходу
За последние годы удалось достигнуть ряда важных достижений, которые уже применяются на практике. К примеру, металлурги начали внедрять гибридные технологии: после печати критической части детали тут же выполняется её механическая доводка, что ускоряет производство и снижает количество дефектов. Также появились расширенные фабрики 3D‑принтеров, где несколько установок выпускают партии сложных запчастей одновременно. Активно развиваются автоматизированные поточные линии, совмещающие печать и постобработку деталей за единый цикл.
Компании переходят к «виртуальному заводскому цеху», где изделия сначала проектируют и тестируют на компьютере и только затем отправляют в производство. Таким образом можно сэкономить на хранении комплектующих и при сбоях в поставках печатать необходимую деталь на месте.
Почему не каждый металл подходит
Не все металлические сплавы одинаково подходят для послойного наращивания. В трёхмерных принтерах широко используют специализированные нержавеющие стали (316L, H13), титановые сплавы (Ti-6Al-4V), никель-хромовые суперсплавы (Inconel, CoCr). Дело в том, что высокоуглеродистые и быстро остывающие материалы при печати обычно трескаются. Например, чистая медь сильно отражает лазерный луч и плохо сплавляется, поэтому, чтобы ей печатать, разрабатывают материалы с особыми легирующими элементами. По тем же причинам, например, к алюминию добавляют кремний, чтобы уменьшить усадочные напряжения.
Отдельно выделяют высокоэнтропийные сплавы — сложные многокомпонентные системы с 5-ю и более основными элементами. Они прочные и термостойкие, благодаря чему повсеместно применяются для 3D-печати.
В России для аддитивных технологий изготавливают металлическую проволоку. Так, на Чепецком механическом заводе (ГК «Росатом») освоили производство порошковой титановой проволоки для промышленной 3D-печати. Изделие применяется в технологиях наплавки, где сплав подаётся в виде проволоки и локально сплавляется. Кроме того, учёные НИТУ МИСИС разработали новый сплав: в нём кальций заменил дорогие редкоземельные элементы, что значительно снизило его стоимость и при этом сохранило высокие прочностные характеристики.
Как печатают металл
Селективное лазерное плавление (SLM) — один из самых распространённых методов: металлический порошок распределяется тонким слоем и по определенным траекториям сплавляется лазером. После наносится новый слой и процесс повторяется. Этот метод обеспечивает очень высокое разрешение печати (толщина слоя порядка 20–80 мкм) и позволяет работать практически со всеми промышленными металлами. Однако SLM обладает рядом ограничений: медленная скорость печати, детали часто требуют поддерживающих конструкций под нависающими участками, для каждого материала нужна своя рецептура сплава, а сам порошок со временем теряет свойства.
Ещё одно перспективное направление — методы прямого подвода энергии и материала (DED). К ним относятся лазерная наплавка порошком и проволокой: LENS (Laser Engineered Net Shaping) позволяет воссоздавать крупногабаритные изделия и ремонтировать детали. Электроннолучевая проволочная наплавка (EBAM) позволяет печатать объёмные конструкции с помощью металлической проволоки и электронных пучков. Такая наплавка отлично подходит для крупных стальных каркасов и корпусных частей, хотя слои получаются толще, чем при SLM.
Струйная печать связующим веществом (Binder Jet) работает иначе: на порошковую заготовку послойно впрыскивают жидкое связующее, прямо как в обычном принтере. Затем порошковую заготовку сплавляют или запекают. Метод особенно эффективен при изготовлении больших литейных опок.
Во многих системах печати уже применяют компьютерное моделирование для подбора оптимальных параметров мощности лазера, скорости сканирования и толщины слоя, что позволяет заранее спрогнозировать структуру материала.
В развитие аддитивных технологий активно включаются крупнейшие российские предприятия. Например, ГК «Росатом Аддитивные технологии». Норникель напечатал крупную литьевую спиральную камеру насосного агрегата для своего комбината — раньше замена этой детали весом около полутонны требовала годового цикла изготовления. Благодаря 3D-сканированию и металлопечати эту операцию удалось выполнить за недели, минуя долгие этапы создания подробных чертежей.
Новолипецкий металлургический комбинат внедрил две промышленные установки 3D-печати песчаных форм: они печатают насосные корпуса, роторы, каркасы и даже десятитонные корпуса спекательных тележек. Изготовление форм удалось ускорить пятикратно, а качество отливок значительно улучшилось.
Кто стоит за инновациями
За развитием аддитивных технологий зачастую стоят университеты и НИИ. Например, в Передовой инженерной школе НИТУ МИСИС впервые в стране научились печатать вольфрам-медные композиты с гироидной структурой. Такой материал открывает возможность создания новых обращенных к плазме компонентов в термоядерной энергетике. В СПбПУ создан Инфраструктурный центр НТИ «Технет» по аддитивному производству, а также впервые в России разработано собственное программное обеспечение для управления металлопринтером. Уральский федеральный университет совместно с индийскими учёными освоил 3D-печать из жаропрочных титановых алюминидов. Новая технология позволяет получать детали, выдерживающие температуру до 700°C при меньшей массе по сравнению с никелевыми аналогами.
Всё не так просто
Главный недостаток аддитивных технологий заключается в том, что промышленные металлические 3D-принтеры стоят в десятки раз дороже обычных станков, а материалы быстро расходуются. Кроме того, невысокой остаётся скорость печати: например, SLM-машины за один час могут наплавить лишь несколько килограммов металла. Это ограничивает использование аддитивных методов в массовом производстве.
Также технологии SLM и EBM требуют сложных поддерживающих структур для деталей с нависающими элементами, они энергоёмкие и чувствительные к свойствам порошка. К тому же порошок со временем разрушается: его мелкие частицы слипаются, что ухудшает качество повторно использованных материалов. Другие методы, такие как Binder Jet, позволяют печатать с большей скоростью, но готовые изделия получаются пористыми и требуют дополнительного спекания.
Всё это — пока нерешённые задачи.
Контроль качества изделий аддитивного производства
Традиционная металлургия развивалась на протяжении многих столетий — от первых способов литья раскалённого металла до современных автоматизированных производств. За это время были разработаны строгие стандарты и требования, которые сегодня закреплены в нормативных документах.
В то же время всё большее значение приобретают аддитивные технологии, чьи изделия находят применение в высокотехнологичных и ответственных отраслях — таких, как аэрокосмическая промышленность, атомная энергетика, медицинское оборудование и другие. В этих областях особенно важен высокий уровень контроля качества.
Для анализа и оценки изделий, созданных с помощью 3D-печати, используются методы, ранее не применявшиеся в традиционной металлургии. Например, компьютерная томография, известная благодаря своему применению в медицине, теперь активно используется для изучения внутренней структуры аддитивных деталей. Это позволяет выявлять микроскопические дефекты и особенности без повреждения самого изделия.
Под изменяющиеся реалии создаются новые профессии. Так, первой в России образовательной программой, которая подготовит специалистов в области стандартизации и метрологии в "аддитивке", стала магистратура «Сертификация изделий аддитивных технологий» в НИТУ МИСИС.
Заводы будущего — уже рядом
Программное обеспечение для оптимизации топологии и прогнозирования свойств материалов, системы «умного завода» с дистанционным контролем, аддитивное прототипирование в сочетании с дополненной реальностью — всё это постепенно входит в практику и скоро станет рутинной частью металлургической отрасли.
Ожидается, что комбинация классической металлургии и аддитивного производства позволит резко повысить технологичность промышленных изделий, снизить их вес и экологический след, а сами металлурги смогут конструировать изделия практически любой формы.
Кремниевые солнечные панели прочно заняли своё место на рынке. Однако путь от кремниевой руды до готового продукта — сложный и трудозатратный. Материал добывают, очищают при температурах свыше 1000 °C, затем выращивают монокристаллы, пилят, шлифуют, осаждают полупроводниковые структуры — часто в вакууме. В итоге получается устройство, преобразующее 20–25% солнечного света в электричество. Эти панели довольно крупные и плохо работают в условиях слабого освещения — например, в пасмурную погоду или на северных широтах.
Несмотря на более чем полувековую историю, применение солнечных батарей в наземных условиях не всегда оправдано. Основная причина — высокая стоимость производства и необходимость постройки новых ЛЭП. Развивающимся странам выгоднее использовать топливные виды энергоресурсов, атомную или гидроэнергетику.
С конца 1980-х годов учёные начали искать более простую и доступную альтернативу — и обратили внимание на перовскиты. Это класс материалов с характерной кристаллической структурой ABX₃: где A — органическая молекула (например, метиламмоний), B — металл (чаще всего свинец), X — галоген (например, йод). Такие соединения обладают особыми фотоэлектрическими свойствами и позволяют создавать солнечные элементы при комнатной температуре с помощью простых растворов солей.
Перовскитные солнечные панели можно собрать всего за 8–10 часов. Технологический процесс включает обработку лазером, кристаллизацию тонких пленок в разреженной среде и нанесение фотоактивных слоёв жидкофазными методами. Причём такие батареи демонстрируют высокую эффективность даже в плохую погоду.
Перовскит в 1839 году на Урале впервые обнаружил немецкий геолог Густав Розе. Название же минерал получил в честь Льва Алексеевича Перовского — русского государственного деятеля, археолога, коллекционера и филантропа — за его вклад в развитие минералогии и геологии в России.
Лев Перовский и Густав Розе
Изначально название «перовскит» применялось к минералам с химической формулой CaTiO₃, а затем распространилось на всю группу подобных соединений. Для создания солнечных элементов используются синтезированные в лабораториях аналоги.
Производство перовскитных солнечных панелей можно максимально автоматизировать с помощью методов напыления как на гибкие, так и на жёсткие поверхности, а также ротационного нанесения типографской печати (струйная или слот матричная печать) — когда раствор материала равномерно распределяется по подложке и формирует однородный слой при вращении. Панель можно напечатать прямо на стекле или пластике, придавая ей любую форму. Это значит, что такие солнечные панели можно интегрировать на поверхность любой кривизны: полностью закрывать ими фасад здания или делать из них витражи. Однако у технологии есть и слабые стороны. Перовскиты чувствительны к воздействию влаги, кислорода, света и высокой температуры. Поэтому сегодня активно ведутся исследования по разработке гибких полимеров, защищающих активный слой от разрушения.
Сегодня этой технологией в пилотном режиме занимаются всего шесть стран в мире, и Россия — одна из них. КПД перовскитных батарей в наземных условиях уже достигает 20%, а их производство существенно менее энергозатратно, чем изготовление кремниевых аналогов. В ближайшие годы мы можем увидеть настоящий технологический прорыв в этой сфере. В Университете МИСИС в 2025 году была защищена первая в России докторская диссертация по технологии получения тонкопленочных перовскитов. Университет уже заключил соглашение с ООО «Графит» о тестировании крышных, оконных и фасадных полноформатных панелей на основе перовскитных фотопреобразователей для энергообеспечения систем умного дома в СберСити.
Вайб-кодинг — это новый подход к созданию программного обеспечения, при котором разработчики формулируют свои задачи на русском, английском или ином естественном языке, а искусственный интеллект генерирует код. В таком формате фокус специалиста смещается на роль проверяющего: он не пишет алгоритм, но тестирует полученные результаты методом проб и ошибок. Подход ускоряет прототипирование — создание первых рабочих версий программ для быстрой проверки идеи на практике — и позволяет создавать собственные приложения даже новичкам, что уже кардинально трансформирует сферу стартапов. Директор Центра технологических конкурсов и олимпиад НИТУ МИСИС Даниил Ефимов объяснил суть вайб-кодинга, его влияние на индустрию, а также рассказал о возможных рисках, связанных с информационной безопасностью.
Что отличает вайб-кодинг?
Вайб-кодинг — это когда разработчик работает на уровне намерений, а не реализации, часто принимая сгенерированный ИИ код без детального анализа. При этом новизна технологии проявляется в двух аспектах. Во-первых, она основательно меняет рабочий процесс разработки: естественный язык становится полноценным интерфейсом для написания кода. Во-вторых, технология упрощает вход в программирование, позволяя даже новичкам создавать приложения без глубоких технических знаний.
Важно отметить, что сам по себе вайб-кодинг возник не на пустом месте. Хотя термин получил популярность благодаря бывшему директору по искусственному интеллекту в компании Tesla и соучредителю OpenAI Андрею Карпати, сама идея программирования через диалог с искусственным интеллектом формировалась и развивалась на протяжении последних трёх лет. Сейчас у индустрии, наконец, появилось чёткое название для явления, которое уже давно набирало силу. И, пожалуй, именно благодаря такой точной формулировке стало проще осознать, почему этот подход оказался столь близким и удобным для разработчиков по всему миру.
Вайб-кодинг и ноу-кодинг — синонимы?
Кроме вайб-кодинга существует ноу-кодинг — это два принципиально разных подхода к созданию программных продуктов, которые часто сравнивают, но редко разграничивают. Суть в том, что оба метода дополняют друг друга, обслуживая разные сегменты пользователей, а не конкурируют между собой. Разработчики взаимодействуют с ИИ-ассистентами, которые генерируют код, но при этом должны обладать пониманием программирования для эффективной верификации результатов. Ноу-кодинг (также известный как low-coding) полезен для начинающих программистов или команд с ограниченным ресурсом на разработку. Ноу-кодинг основан на визуальном моделировании с использованием уже существующих библиотек алгоритмов, которые будут выполняться каким-то готовым приложением. То есть, пользователь не всегда взаимодействует с кодом напрямую или сводит это к минимуму. Хотя уже сейчас понятно, что вайб-кодинг может стать стимулом для роста ноу-кодинг рынка и ускорить популяризацию этого формата.
Ресурсы для вайб-кодинга
Современная экосистема сервисов для вайб-кодинга включает в себя несколько ключевых категорий:
● большие языковые модели (LLM),
● редакторы кода с интеграцией LLM,
● голосовые интерфейсы,
● платформы для быстрой генерации простых проектов и сайтов,
● инструменты автоматической проверки и тестирования кода.
Самое быстрое погружение в вайбкодинг возможно с помощью разных «однокнопочных» сервисов, где можно буквально с одного запроса реализовать простое приложение прямо в браузере — среди таких можно попробовать Google Firebase Studio, bolt.new или same.new. Также можно попробовать классические режимы чата с LLM, то есть как обычно просто написать LLM «помоги создать мне приложение, которое будет уметь…». Для таких целей среди российских LLM можно попробовать Yandex GPT 5 и GigaChat 2.0 от Сбера. Зарубежные аналоги — DeepSeek, ChatGPT-4o (OpenAI), Claude 3.7 Sonnet (Anthropic). Но они подходят, если вы уже разобрались «куда копировать код», чтобы он работал. А если не разобрались, то они же и помогут это сделать. И если хочется максимально ускорить процесс вайбкодинга, то можно использовать нейросети прямо в редакторе кода. Для этого активно используются Cursor, GitHub Copilot, Tabnine, а в России — SourceCraft Code Assistant от Yandex Cloud и GigaCode от GitVerse (включая IDE GigaIDE). А для ускоренной генерации лендингов с помощью ИИ применяются платформы вроде Framer AI и Tilda AI.
Несмотря на быстрый рост и разнообразие решений, индустрия вайб-кодинга сталкивается с рядом технологических ограничений:
● Современные LLM не всегда сохраняют контекст проекта на протяжении всей сессии, что приводит к переписыванию или поломке ранее сгенерированного кода.
● Нередко модели «забывают» о частях задачи, и разработчику приходится вручную уточнять и дополнять командами.
● LLM не гарантируют защиту от уязвимостей, особенно в сложных проектах, где требуется глубокий опыт программирования.
● Автоматизация взаимодействия с Git и аналогами пока ограничена, что снижает удобство работы в команде.
● Хотя технология уже позволяет автоматизировать тестирование, интерфейсы и сервисы для вайб-кодинга пока не сделали этот процесс полностью удобным и автоматическим. Нужно дорабатывать запросы к нейросети и объяснять ИИ, что именно ты хочешь протестировать.
Что уже умеет вайб-кодинг и какие у него перспективы
Одним из наиболее востребованных применений вайб-кодинга стало прототипирование. Многие стартапы прибегают к этому методу для быстрой сборки минимально жизнеспособных продуктов (MVP), которые позволяют протестировать гипотезу на ранней стадии. Классические методы проверки концептов, такие как «Волшебник из страны Оз» и «Фальшивая дверь», позволяют тестировать идеи с минимальными ресурсами. В первом случае функционал продукта имитируется вручную: например, пользователь взаимодействует с интерфейсом, не зная, что «за кулисами» операции выполняет человек, а не алгоритм. Во втором — создается фиктивный элемент (кнопка, страница), который не несёт никакой функции, но собирает данные о спросе пользователей. С появлением нейросетей к этим методам добавился третий — генерация прототипов с помощью ИИ. Нейросети автоматически создают рабочие версии продукта на основе описания, сокращая время разработки с недель до часов.
Доступным стало использование кода в кустарных проектах и софте для личного пользования. Например, если вам давно хотелось сделать приложение для учёта продуктов в холодильнике — вайб-кодинг позволяет реализовать такую идею буквально за один-два вечера. Вайб-кодинг позволил мне быстрее прототипировать идеи и проверять концепты. Например, когда нужно доработать визуальную часть готового решения, чтобы показать заказчику, как будет выглядеть итоговый продукт, я оперативно вношу правки с помощью ИИ. А ещё с нейросетями я создаю личные проекты: то, что раньше разрабатывал за неделю, теперь делаю за пару вечеров — просто описываю задачу, а ИИ генерирует код.
Однако метод вызывает серьёзные опасения относительно утечки информации, поддержки ПО после его запуска и потенциальной потери разработчиками фундаментальных навыков программирования. Будущее, вероятно, будет включать гибридный подход, который сбалансирует преимущества как традиционных методов, так и вайб-кодинга.
Отдельно эксперты отмечают образовательный потенциал данного метода. Сегодняшняя система обучения только начинает осмысливать, как интегрировать LLM в учебный процесс. Если в гуманитарных дисциплинах — филологии, лингвистике — уже идут активные обсуждения по поводу академической добросовестности, то в области программирования вайб-кодинг позволяет изучать логику кода, подходы к решению задач и архитектуру приложений.
Кроме того, вайб-кодинг позволяет автоматизировать задачи, выходящие за рамки классического программирования. Например, с его помощью можно быстро составить SQL-запрос — специальную команду для работы с базой данных, которая позволяет извлекать нужную информацию, — написать формулу для Excel или решить уникальную задачу, связанную с конкретным рабочим контекстом.
И, наконец, наиболее стремительно развивающееся направление — корпоративный вайб-кодинг. Уже сейчас компании рассматривают интеграцию LLM как способ оптимизации процессов, ускорения разработки и повышения эффективности команд. Самый оптимистичный экономический эффект по прогнозам будет достигнут именно в B2B-сегменте — когда инструменты вайб-кодинга начнут использоваться внутри организаций на постоянной основе.
Если заглянуть в будущее, можно представить, как в какой-то момент современные технологии вайб-кодинга пересекутся с нейроинтерфейсами. Такой симбиоз способен создать принципиально новые сценарии: от проектирования архитектуры программ исключительно с помощью мысли до интеллектуального тестирования, основанного на ментальном моделировании пользовательских сценариев. Одним из перспективных направлений уже сегодня становятся так называемые AI-агенты — интеллектуальные системы, способные брать на себя комплексную автоматизацию всего цикла разработки.
Советы, если хотите попробовать себя в вайб-кодинге
● Освойте основы промпт-инжиниринга. Умение правильно формулировать запрос к ИИ — ключ к получению нужного результата. Например, вместо абстрактного «создай сайт для отображения погоды» лучше написать «создай адаптивное одностраничное приложение с использованием React, которое отображает данные о погоде из внешнего API».
● Учитывайте ограничения контекста. Большие языковые модели имеют ограниченное «контекстное окно» — они могут забывать, что было написано ранее, особенно при работе над сложным проектом. Один из лайфхаков — использовать отдельные чаты для разных модулей или этапов разработки.
● Освойте базовую отладку. Даже самые продвинутые LLM могут ошибаться — например, предлагать устаревшие команды установки библиотек или неверные названия модулей. Иногда быстрее самостоятельно найти и устранить ошибку, чем долго пытаться исправить её с помощью ИИ.
● Выбирайте подходящий стек технологий. Теоретически, вайб-кодить можно на любом языке — хоть на C++. Но если уровень подготовки невысок, лучше отдать предпочтение более простым и распространённым технологиям, таким как JavaScript, где легко найти документацию и примеры.
● Разбирайтесь в том, что создаёте. Вайб-кодинг — прекрасный способ увидеть, как реализовываются ваши идеи в коде. Следите за тем, какой код генерирует ИИ, и пытайтесь понять, как он устроен. Это поможет не только улучшать результат, но и постепенно развивать собственные навыки программирования.
Главное преимущество вайб-кодинга — практически полное отсутствие порога вхождения. С его помощью можно создать простое работающее приложение, даже не обладая серьёзными знаниями в программировании. Однако эффективность работы напрямую зависит от того, как вы взаимодействуете с нейросетью и какие инструменты выбираете. Например, недавно был кейс, когда блогер в твиттере создал веб-сервис с монетизацией с помощью вайбкодинга и у него появились реальные клиенты, но т. к. он был без бэкграунда создания каких-либо продуктов, то очень скоро его сервис взломали и его пришлось закрыть. Но мы точно знаем, что вся эта концепция точно не хайп и она найдёт свое применение на рынке, будет появляться все больше новых сервисов, классных историй успехов и провалов. Так что если у вас всегда было желание овладеть магией программирования хоть чуть-чуть, то сейчас самое время потратить на это пару вечеров и создать ваш уникальный сервис. Кто знает, вдруг тыква превратится в карету?
Сегодня, 14 апреля, отмечается Всемирный квантовый день. Квантовые технологии перестали быть научной фантастикой и уже сегодня меняют реальные отрасли — от медицины до финансов. Директор дизайн-центра квантового проектирования НИТУ МИСИС Наталия Малеева расскажет как Россия вошла в тройку мировых лидеров в этой гонке, какие задачи решают отечественные квантовые компьютеры и где их применяют уже сейчас.
Последние годы стали переломными в мире квантовых технологий. Сделав первые шаги в области индустриальных применений, они перестали быть только лабораторной игрушкой, интересной лишь ученым.
Сейчас основные потребители на рынке квантовых вычислений – здравоохранение, банковский и финансовый сектор, производство, автомобилестроение и химическая промышленность. Глобальный рынок квантовых технологий небольшой, но хорошо развивающийся: по разным оценкам в ближайшие 10 лет ожидается совокупный среднегодовой темп роста до 34%. По данным McKinsey к 2035 мировой рынок квантовых технологий оценивается от 28 до 72 млрд долларов США; квантовых коммуникаций – от 11 до 15 млрд долларов США; и квантовых детекторов – от 0.5 до 2.7 млрд долларов США. Предполагается, что российский рынок может занять до 6% от глобального.
Мы находимся сейчас на этапе так называемых NISQ-устройств (Noisy intermediate-scale quantum – шумные квантовые устройства, порядка нескольких сотен кубитов), уже решены некоторые задачи квантовой химии, выполнены пилотные алгоритмы, сделаны первые шаги в квантово-классическом машинном обучении и решены проблемы оптимизации.
Многокубитные квантовые компьютеры созданы во многих странах на основе разных физических носителях. На сегодняшний день в России созданы 60-кубитный квантовый компьютер на основе фотонных чипов, 50-кубитный квантовый процессор на ионах, 50-кубитный на нейтральных атомах, 16-кубитный сверхпроводниковый универсальный квантовый процессор и 16-кубитный сверхпроводниковый квантовый симулятор. Только две страны, кроме России развивают все эти платформы, это США и Китай. То, что мы входим в тройку мировых лидеров – колоссальное конкурентное преимущество, ведь пока нельзя говорить об однозначном доминировании одной из физических платформ для квантовых вычислений.
Ряд процессоров и в мире, и у нас уже применяют для практических расчетов. Предоставлен облачный доступ к расчетам на таких компьютерах, и уже можно попробовать свои силы в написании программ. В нескольких странах,включая Россию, созданы сети из квантовых линий связи. Они помогают защищать передаваемую информацию на уровне законов физики и не поддаются перехвату и расшифровки злоумышленниками. Они находят реальное применения в государственных и банковских структурах. В России на данный момент созданы и работают в тестовом режиме протяженные квантовые сети. В планах протянуть эти линии на расстояния свыше 10000 км.
Если делать прогноз на ближайшие 10 лет, то наибольшую пользу квантовые вычисления продолжат приностить финансовому сектору (например, оптимизация финансовых портфелей), здравоохранению (например, анализ снимков или фармакологические исследования), энергетике и ЖКХ (например, решение задач оптимизации выработки и распределения электроэнергии), автомобилестроению (оптимизация производственных процессов и логистики).
Квантовая сенсорика уже востребована, и станет еще более популярной. Например, в калибровке стандартов для новых технологий связи и повышения точности геолокации, в медицине при сканировании мозга и отслеживании метаболических процессов в реальном времени. Она востребована и для наблюдений за окружающей средой при прогнозирование извержений вулканов и землетрясений.
Разработки в области квантовой коммуникации лягут в основу не только модульной архитектуры квантовых процессоров следующих поколений, но и будут востребованы в области киберзащиты от злоумышленников, т.н. пост-квантовая криптография.
17 редкоземельных металлов (РЗМ) — это дорогие и востребованные элементы, без которых невозможно создание наукоёмких технологий в медицине, микроэлектронике, металлургии, машиностроении, зелёной энергетике, а также в аэрокосмической и оборонной отраслях. Их даже называют «витамины промышленности», потому что они всё делают лучше, прочнее, долговечнее, устойчивее. Почему же эти элементы называют «редкими», если их добывают тоннами? Вместе с доктором технических наук, заведующим кафедрой цветных металлов и золота НИТУ МИСИС Вадимом Тарасовым сейчас разбёремся, откуда вокруг них такой ажиотаж.
Кто первый нашёл редкоземельные металлы и почему их добыча такая дорогая?
РЗМ — это, как правило, электропроводные и пластичные металлы серебристо-белого цвета. Несмотря на название, эти элементы разбросаны в земной коре повсюду, просто они не попадаются в концентрированной и экономически выгодной форме. Термин «редкоземельные» (от лат. terra rara) был ввёден в обиход в 18 веке, когда РЗМ были обнаружены как компоненты сложных оксидов, которые в то время назывались «землями» (от лат. terra), ну а «редкими» (от лат. rara) их прозвали, поскольку никогда раньше не видели и считали не распространёнными.
В науке есть схожее по звучанию понятие, но путать их не надо. Есть распространённые, но труднодобываемые редкоземельные металлы — группа из 17 элементов: скандия, иттрия и 15 лантаноидов (лантан, самарий, лютеций, диспрозий, гольмий, эрбий, празеодим, тулий, церий, диспрозий, иттербий, тербий, неодим, европий, прометий).
А есть 18 редких металлов, которые и правда почти не встречаются в земной коре. Четыре из них можно получить после обогащения руд: бериллий, ниобий, литий, тантал. Ещё 14 называют попутными микрокомпонентами — рассеянными редкими металлами и 5 радиоактивных редких металлов.
Финский химик Юхан Гадолин в 1794 году открыл первый химический элемент группы редкоземельных металлов — иттрий — в минерале иттербите, позже переименованном в гадолинит. А сам минерал обнаружили шахтеры шведской деревни Иттерби, отсюда и название.
Вообще, добыча и переработка РЗМ очень дорогая, так как их часто обнаруживают рассеянными в низких концентрациях. Чтобы получить большое количество вещества, требуются огромные ресурсы и крупномасштабные операции. Очистка редкоземельных элементов тоже энергоёмкий и химически сложный процесс, где задействованы вредные вещества, такие как концентрированные кислоты. Да и сама руда, из которой они добываются, часто содержит радиоактивный торий и уран.
Некоторые редкоземельные металлы ведут себя крайне непредсказуемо. На воздухе при комнатной температуре они медленно тускнеют, а при контакте с холодной водой образуют гидроксиды и выделяют водород. При взаимодействии с паром они быстро превращаются в оксиды, а при нагреве до 500 °C самовозгораются. Подобное разнообразие состояний превращает их переработку и хранение в технологически сложную задачу.
На фоне своих «соседей» по элементной таблице особо выделяется прометий. Это нестабильный радиоактивный элемент, он практически не встречается в природе, а производится лишь в ядерных реакторах. В 1920-х гг. итальянские учёные заявили, что открыли новый 61 элемент — флоренций, а в Иллинойсском университете США объявили, что 61 элемент — это иллиний. Но все оказались неправы. В 1945 г. химики Д. Маринский, Л. Гленденин и Ч. Кориэлл получили новое вещество из продуктов деления урана, и спустя 5 лет за № 61 закрепилось имя «прометий». Благодаря чистому бета-излучению он использовался в радиоактивных батарейках, вакуумных контактах (герконах), а сейчас исследуется как замена актиния в противораковых препаратах. На Земле содержится всего лишь несколько сотен граммов этого элемента.
Какие редкоземельные элементы наиболее востребованы?
Наиболее востребованы в промышленности неодим, празеодим (дидим) и самарий — для создания мощных постоянных магнитов. Ещё эти металлы, а вернее их оксиды, улучшают свойства сверхпроводников, стекла и сплавов, используется в лазерах и для получения пигментов. Остальные РЗМ нужны для производства аккумуляторных батарей, специальных сплавов, ветрогенераторов, ядерных реакторов, катализаторов в нефтепроме, жидкокристаллических дисплеев, радаров, керамики и т. д.
Магниты на основе неодима и самария являются самыми мощными. Они широко применяются во многих отраслях науки и техники, а также в быту: в магнитно-резонансных томографах, металлоискателях, жёстких дисках для компьютеров и др. Без них невозможно представить альтернативную энергетику, ведь РЗМ содержащие магниты — ключевой компонент электродвигателей и генераторов ветряных турбин. Благодаря высокой силе сцепления с металлами РЗМ содержащие магниты могут удерживать предметы, которые превышают их собственный вес в 100 раз. Неодимовые магниты, кстати, можно найти в домашних аксессуарах, они используются в креплениях для штор, держателях ножей, магнитных застёжках сумок или даже в игрушках (например, конструкторах типа Neocube).
У какой страны самый большой запас?
РЗМ встречаются по всему миру почти в половине месторождений. Значимое количество редкоземов содержится примерно в 250 минералах, но в качестве руд экономически целесообразны лишь некоторые из них: бастнезит, монацит, ксенотим, эвдиалит и лопарит. Кроме того, источником ценных элементов являются обогащённые глины. Церий, например, находится на 25-м месте по распространённости в мире, что ставит его на один уровень с медью. За ним следуют лантан и неодим; они встречаются в тех же объёмах, что и свинец.
Первое место по объёму добычи и поставкам редкоземельных металлов занимает Китай — здесь извлекают и перерабатывают от 65 до 80% всех РЗМ. Дальше в рейтинге: США, Австралия, Мьянма, но их суммарные запасы дают всего около 24%. Россия занимает 7 место по добыче. Единственным источником редкоземельного сырья в России является лопаритовый концентрат, производимый из руд Ловозерского месторождения в Мурманской области, который перерабатывается на Соликамском магниевом заводе.
В настоящее время годовая потребность российской экономики в редкоземельных металлах составляет около 2000 тонн, а концу 2026 года возрастёт до 10 000 тонн. Основными сферами потребления РЗМ в России являются: оптическое производство и полировальные порошки; производство катализаторов для нефтепереработки, химической промышленности, автокатализаторов; металлургия, производство керамики; лабораторные реактивы, а также фармацевтика, электроника, искусственные кристаллы, люминофоры, постоянные магниты.
На 2025 год Россия занимает 1% рынка редкоземельного сырья. По запасам РЗМ мы занимаем 2-е место в глобальном рейтинге с показателем в 28,5 млн тонн. Крупнейшие месторождения: Ловозерское месторождение (Мурманская область), Томторское месторождение (Республика Саха, Якутия), Холтосонское месторождение (Забайкальский край), Ковдорское месторождение (Мурманская область), Фёдорово-Панский массив (Мурманская область), Хибинская группа месторождений (Мурманская область). Изучением запасов редкоземельных металлов занимается Всероссийский научно-исследовательский институт минерального сырья.
Где применяются редкоземельные элементы?
Знаете, почему некоторые смартфоны такие дорогие? Для их производства необходимы 9 редкоземельных элементов:
гадолиний — в дисплеях, динамиках и электронных схемах,
диспрозий — добавка в магниты электросхем для сохранения свойств при нагреве и температурных перепадах,
европий — для красного светящегося вещества дисплея,
иттрий — для дисплеев, светодиодов,
лантан — в электронных схемах, дисплее, шлифованном стекле, для оптических линз,
неодим — магниты в схемах и динамиках из сплава с железом и бором,
празеодим — добавка в неодимовые магниты, дисплей, динамик,
тербий — для зелёного люминесцирующего вещества на дисплее, в динамиках, схемах и вибрационном механизме для защиты мини-магнитов от высоких температур,
церий — для шлифованного стекла.
Можно ли заменить их более дешёвыми металлами? Конечно! Но это ухудшит цветовое отображение на дисплее, увеличит вес гаджета, снизит скорость работы и устойчивость к перегреву.
Тот же церий выделяют из смеси элементов процессами экстракции и хроматографии, а потом электролизом расплава CeF3 (фторида церия). Церий в быту применяется в каталитических покрытиях духовок и стёклах печей. При нагреве он ускоряет разложение жира и органических загрязнений, упрощая уход за техникой.
В течение многих лет иттрий и европий использовались в качестве люминофоров, которые помогали нам видеть красный цвет на ламповых телевизорах. Соединения гадолиния и тербия использовались для получения жёлто-зелёных люминофоров. При добавлении в состав очень небольшого количества этих редкоземельных элементов цвета на экране получались яркими и приятными для глаз.
Наиболее необычное применение РЗМ — в технологиях борьбы с контрафактом. Особые соединения редкоземельных элементов отражаются в ультрафиолетовом свете, благодаря чему они особенно полезны при выявлении поддельной валюты.
Лантан (La) улучшает оптические свойства стекла, уменьшая искажения. Его добавляют в линзы дорогих фотоаппаратов, биноклей и даже антибликовых очков. Оксиды церия (Ce) или лантана (La) иногда включают в солнцезащитные кремы для поглощения УФ-лучей.
Празеодим (Pr) используется в стеклах сварочных масок и специальных очках, блокируя вредное инфракрасное излучение. Иногда его добавляют в декоративное стекло для получения желто-зеленых оттенков.
Самарий (Sm) входит в состав сплавов для кремней зажигалок. Такие кремни долговечны и дают устойчивую искру даже после тысяч использований.
Некоторые ткани пропитывают соединениями РЗМ для УФ-защиты или антибактериальных свойств. Например, спортивная одежда может содержать церий (Ce) для нейтрализации запахов.
Иттрий (Y) повышает термостойкость керамики. Его добавляют в посуду, рассчитанную на экстремальные температуры, например, в формы для выпечки или горшки для медленного приготовления пищи.
Редкоземельные металлы окружают нас повсюду — от смартфонов до энергосберегающих ламп. Их необычные свойства делают бытовые устройства компактнее, эффективнее и долговечнее. Теперь вы узнали о них чуточку больше.
В первое воскресенье апреля в России отмечается День геолога. Геология играет ключевую роль в понимании планеты, обеспечивает нас необходимыми ресурсами и позволяет предсказывать природные катастрофы. Сегодня эти учёные используют технологии, которые ещё недавно казались фантастикой. Одна из самых удивительных — мюонография, позволяющая буквально «просвечивать» Землю с помощью частиц из космоса и изучать структуры недр, гор, вулканов, а также получать уникальные данные о залегании полезных ископаемых, которые традиционные способы не могут выявить.
Космические шпионы
Мюоны (мю-мезоны) — это элементарные частицы, которые рождаются при столкновении космических лучей с ядрами атомов в атмосфере. Они могут проходить сотни метров сквозь крупные объекты и проникать вглубь земли. Впервые их обнаружили в 1936 году, но только в XXI веке, с появлением сверхчувствительных детекторов и мощных компьютеров, технология вышла на новый уровень. Каждую минуту на квадратный метр Земли падает 10000 мюонов. Часть из них поглощается, проходя через материалы и вещества с разной плотностью. Метод мюонографии основан на фиксации непоглощенных частиц детектором. Принцип похож на рентгенографию, но не требует радиоактивных источников излучения и подходит для огромных объектов километровых размеров. Сравнивая потоки мюонов, можно исследовать самые разные крупные природные и промышленные объекты, не только горы, но и египетские пирамиды или древнерусские монастыри, объекты горнодобывающей отрасли и др.
Различают два метода: мюонография и томография мюонного рассеивания. Первый использует детекторы, размещенные снизу или сбоку от объекта, чтобы фиксировать мюоны, которые проходят через него. Второй регистрирует двумя детекторами (сверху и под объектом, например, на таможне) изменение углов движения мюонов, прошедших через исследуемый объект. Наилучшим угловым разрешением обладают автономные детекторы на основе ядерной фотоэмульсии. Они способны обнаружить объекты размером 15 метров на расстоянии 1 км, а на меньших дистанциях — участки с изменением плотности от 50 см. Оба метода экономически выгодные и экологически безопасные, но имеют разные сферы использования.
Пирамиды, монастыри и тайные комнаты
Самые резонансные открытия современной мюонографии связаны с исследованием памятников архитектуры. В 2016 году международная группа ученых обнаружила в пирамиде Хеопса в Египте новый коридор длиной в 30 метров и диаметром 8 метров. Это первое крупнейшее открытие с 19 века в истории изучения пирамид.
Международная группа ученых исследует пирамиду Хеопса
В России мюонографию развивают ученые НИТУ МИСИС и Физического института им. П. Н. Лебедева РАН. Один из проектов был реализован в крепости Нарын-Кала в Дербенте, которая входит в список Всемирного наследия ЮНЕСКО. Физики исследовали засыпанное на 10-метровой глубине сооружение — предположительно, древнейший христианский храм на территории России.
Крепость Нарын-Кала в Дербенте
Кроме того, совместно с Комиссией по работе с вузами и научным сообществом при Епархиальном совете г. Москвы с использованием эмульсионных детекторов в подвалах Церкви Похвалы Божьей Матери Свято-Троицкого Данилова монастыря нашли две скрытые пустые комнаты, неизвестный воздуховод и другие особенности замурованных подвалов церкви. На территории монастыря между зданиями двух церквей обнаружены большие подземные полости. Ученые предполагают, что это могут быть древние крипты, но их происхождение и назначение еще предстоит изучить. Эти выдающиеся исследования были удостоены Макарьевской премии 2022 года в области естественных наук.
Исследование Свято-Троицкого Данилова монастыря в Переславле-Залесском
Мюонографические исследования в России продолжаются. В 2023 году в Свято-Успенском Псково-Печерском монастыре между Братской и Троицкой улицами российские ученые снова обнаружили неизвестные ранее помещения пещерного храма —большой склер и коридор на входе в храм.
В 2024 году закончено исследование территории Спасо-Каменного монастыря в Кубенском озере Вологодской области. Обнаружено несколько подземных полостей на глубинах до 3,5 метров, одна из которых может быть захоронением 16 века митрополита Варлаама – единственного митрополита, похороненного не в Кремле. Обнаружение этих особенностей поможет предотвратить их повреждение в ходе планируемых работ по восстановлению взорванного в 1937 году Преображенского храма монастыря.
Геологоразведка и безопасность
В горнодобывающей промышленности мюонография совершает настоящую революцию. Традиционные методы разведки требуют взрывных работ, значительных временных затрат и множества скважин — все это очень дорого, требует длительного времени и дает достаточно точной информации.
В 2021 году канадский стартап Ideon Technologies впервые применил компактный скважинный детектор мюонов для сканирования уранового месторождения под 600-метровой толщей песчаника на руднике McClean Lake в Саскачеване. Детектор диаметром менее 10 см и мощностью 10 Вт сочетает мюонографию с ИИ-анализом данных, значительно повышая точность поиска рудных тел и сокращая экологический ущерб. По словам экспертов, метод превосходит традиционную геофизику в обнаружении глубокозалегающих месторождений, что подтвердили и проекты в Селлафилде (Великобритания) и на «Фукусиме-1».
В конце 2024 года ученые АО «ГНЦ РФ ТРИНИТИ» успешно протестировали прототип мюонного детектора, предназначенного для работы в скважине при разведке твердых полезных ископаемых. В будущем он позволит анализировать изменения потока мюонов и создавать трехмерные модели подземных структур, выявляя месторождения руд и других ценных ресурсов. Разработка открывает новые возможности для неразрушающей геологоразведки, снижая затраты на бурение и повышая точность поиска.
Мюонография становится также бесценным инструментом для обеспечения безопасности социальных агломераций. В Японии технологию используют для контроля состояния затопленных реакторов «Фукусимы». В Италии с её помощью изучают динамику магматического столба под Везувием, состояние древних сооружений в Риме.
Будущее уже здесь
Мюонографические исследования — эффективный, экономичный и экологически безопасный способ исследований и мониторинга внутренней структуры крупных природных, культурных и промышленных объектов. Метод определяет разность плотностей горных пород в межскважинном пространстве и повышает уровень изученности недр, что позволяет геологам строить более детальные трехмерные модели массива и минимизировать последствия возможных природных и техногенных катастроф для населения, инфраструктуры и окружающей среды.
Задумывались ли вы о том, почему медицинские изделия выглядят именно так, а не иначе? Почему, например, одно выполнено в форме цилиндра, а другое вытянутое и плоское? За созданием современной техники в ведущих организациях стоят не только инженеры, но и профессиональные промышленные дизайнеры. Расскажем, как в НИТУ МИСИС с 2024 года магистранты программы «Промдизайн и инжиниринг» создают функциональный и эргономичный дизайн для университетских разработчиков инновационной биомедицинской техники.
По словам директора Института биомедицинской инженерии НИТУ МИСИС Федора Сенатова, это первая среди российских университетов коллаборация биоинженеров и промдизайнеров. Она стала важным шагом для производства медицинских изделий, где инженеры, ученые и дизайнеры проходят совместно весь цикл разработки. Такой подход позволяет выпускать специалистов будущего — инженеров «М-типа», то есть мультидисциплинарных. Наладить подобное сотрудничество было нужно, потому что дизайнерские решения влияют на восприятие медицинских устройств в клинической практике. Эргономичная конструкция не только функциональна, но и эстетична. Уже этим летом студенты передовой инженерной школы МИСИС направления «Биомедицинская инженерия и биофабрикация» выйдут на защиту дипломных проектов, созданных при участии коллег креативной программы.
«Мы хотим вывести медицинские разработки вуза на новый уровень, визуально усовершенствовать их для конечных потребителей – врачей. Ведь именно им должно быть удобно и приятно работать с устройствами. Инженеры создают технологичное и полезное изделие, но пренебрегают взаимодействием с дизайнерами, а зря. Ведь коллеги учитывают множество дополнительных факторов и помогают сделать конкурентоспособный и стильный проект», – добавил доцент Института биомедицинской инженерии, ментор магистерской программы «Промдизайн и инжиниринг» НИТУ МИСИС Владислав Львов.
Дизайнеры проходят все стадии концептуального проектирования: дизайн-исследование, эскизный поиск, эргономику, пользовательский сценарий, поиск форм-фактора и цвета. Также инженеры с технической точки зрения узнают, какие детали можно убрать, а какие точно оставить. Например, в 2023 году ученые НИТУ МИСИС представили первый «тканевой пистолет», сшивающий раны биополимерами. Устройство предназначено для использования на этапах эвакуации. Студенты-биоинженеры и дизайнеры оптимизировали его для домашних условий – аптечки. Есть и проекты-фантазии: как с учетом технологического прогресса устройства будут выглядеть через несколько лет.
«Научные открытия привели к появлению новых технологий, материалов и методов, а дизайн сделал эти инновации более удобными для людей, – делится руководитель магистерской программы Университета МИСИС «Промдизайн и инжиниринг» Елена Пантелеева. – Будущее за осознанным проектированием, в котором заложена синергия компетенций в инженерии и дизайне. Всё это, в конечном счете, повышает качество продукта и улучшает пользовательский опыт».
По словам Елены, дизайнер работает с эмоциями потребителя, в то время как инженер сконцентрирован на технических аспектах. Пациентам приятнее видеть лаконичное оборудование. При проектировании любого устройства нужно учитывать технические и производственные требования: функциональность, экономичность конструкторского решения, рациональное использование материалов и пространства. Промдизайнеру не так важно уметь рисовать, как владеть навыками технического рисунка, 2Д- и 3Д-моделирования. На стыке творчества и инженерных задач нужно обладать развитой насмотренностью, разбираться в инновационном сырье, цветах, фактуре, технологиях. Помимо этого, вывод изделия на рынок – вопрос экономический. Любой продукт должен быть конкурентоспособным и, желательно, лучше аналогов. Промышленный дизайнер следит за трендами, адаптирует их под свою нишу и решает бизнес-задачи. Междисциплинарный подход помогает промдизайнерам комплексно представить проблему, с которой может столкнуться пользователь, и создать профессиональное решение под запрос потребителя.
Пример для наглядности: